在制造业中,精益单元线设计(Lean Cell Design)是提升效率、减少浪费和增强生产柔性的核心方法。结合“动力线”(通常指高功率设备供电或生产动力单元)的需求,以下是打造高效、柔性动力线的关键策略:
一、精益单元线设计的基本原则
价值流导向:明确动力线服务的核心价值流(如电机装配、电池生产等),消除非增值步骤(如过度搬运、等待)。
单件流(One-Piece Flow):通过小型化、模块化设计,减少批量生产,缩短动力设备的供电或传动距离。
标准化与柔性化平衡:标准化动力接口(如电压、连接器),同时保留快速切换(SMED)能力以适应多品种生产。
二、高效动力线设计的关键策略
1. 布局优化
U型或直线型单元布局:缩短动力传输路径,减少线缆或传动损耗。
人机工程学:避免动力线(电缆/管道)交叉干扰,确保维护便捷性。
2. 动力系统柔性化
模块化供电设计:如可插拔式电缆、标准化电源接口,支持设备快速重组。
智能配电:使用变频器、软启动器动态调整动力输出,匹配不同负载需求。
3. 自动化与数字化
传感器集成:实时监测电流、电压、温度,预防过载故障。
数字孪生:虚拟仿真动力线布局,优化能耗和效率。
4. 精益工具应用
5S管理:规范动力线周边环境(如电缆槽整理),减少安全隐患。
TPM(全员生产维护):定期保养动力设备(如电机、变压器),避免突发停机。
三、柔性动力线的实现路径
快速换型(SMED):动力线的切换时间压缩(如更换模具时同步调整供电参数)。
多能工培训:操作员掌握动力设备基础维护技能(如电缆连接、故障复位)。
拉动式生产(Pull System):根据下游需求动态调节动力供应,避免空载运行。
四、世豪动力线案例参考
将传统打包工序升级为动力线(自动化/半自动化动力驱动生产线),可以显著提升效率、柔性和整体竞争力。
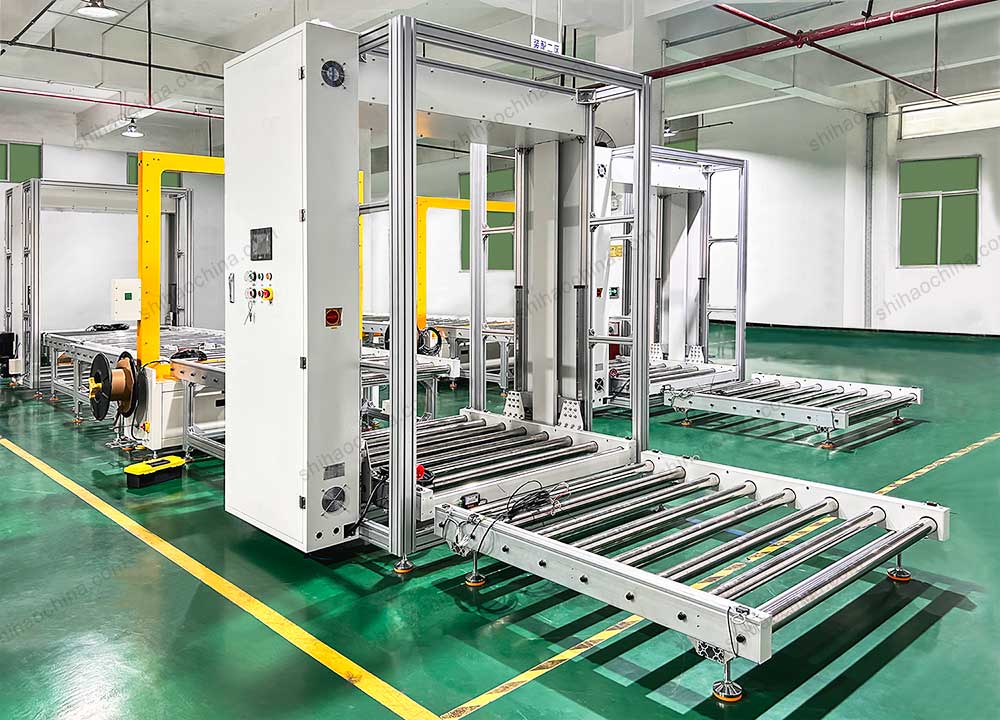
一、打包工序升级为动力线的核心优势
1. 效率大幅提升
自动化打包:动力线集成自动封箱机、捆扎机、贴标机等设备,减少人工操作时间,速度提升30%~50%。
连续流生产:消除传统打包中的等待、搬运浪费,与上游工序(如装配、分拣)无缝衔接。
案例:电商仓储中,动力线打包系统可实现每分钟处理20~30件包裹,远超人工的5~10件。
2. 柔性化生产适应多品种需求
快速换型:动力线可通过程序切换(如调整打包尺寸、捆扎力度)适应不同产品规格(如小件快递 vs 大件工业品)。
模块化设计:按需增减功能模块(如增加称重、扫码单元),支持未来业务扩展。
3. 质量稳定性增强
标准化作业:动力线消除人工打包的松紧不一、标签错贴等问题,合格率可达99%以上。
实时检测:集成视觉系统或传感器,自动识别漏装、包装破损等缺陷。
4. 成本优化
人力节省:1条动力线可替代5~8名工人,长期成本更低。
能耗控制:智能启停技术(如空载时自动断电)减少电力浪费。
5. 安全性与人机协作
降低工伤风险:减少人工搬运重物、接触锋利包装材料的机会。
人机协同:动力线可设计为“人工辅助+自动传输”模式,平衡效率与灵活性。
二、升级为动力线的关键技术方案
1. 动力传输系统选择
电动滚筒输送线:适合轻型包裹,噪音低、易维护。
链条/皮带驱动:适用于重型或不规则物品打包。
2. 核心设备集成
自动折箱机 → 自动装填 → 封箱机 → 捆扎机 → 贴标/扫码 → 分流输送。
可选附加功能:自动称重、体积测量、3D视觉定位。
3. 智能控制与数据联动
PLC+上位机控制:实现设备协同和参数远程调整。
与WMS/ERP对接:自动获取订单信息,动态调整打包规则(如优先发货标签)。
三 、更多行业可行性
食品行业:动力线实现箱内自动填充缓冲材料,避免运输破损。
快递分拣中心:动态调整打包尺寸,减少包装材料浪费30%。
制造业:与AGV联动,实现成品自动打包入库。
打包工序动力线升级的核心价值:
✅ 效率:从“人推货”变为“货动人不动”;
✅ 柔性:一键切换应对多品种、小批量趋势;
✅ 数据化:打包过程可追溯,支持持续优化。
若需具体方案设计或设备选型建议,可进一步提供场景细节(如产品类型、日均产量等)!